This chapter summarizes the building performance approach to be used for compliance. It includes a discussion of the alternative calculation methods, the procedures involved in determining the energy budget of the Standard Design and the energy use of the Proposed Design Building, and how to plan check performance compliance documentation. The basic procedure is to show that the Time Dependent Valuation (TDV) and source energy use of the proposed design are less than or equal to the TDV and source energy budget of the standard design. The standard design is a building with the same geometry as the proposed design, but the envelope, lighting and mechanical features are defined by the mandatory and prescriptive requirements of the Building Energy Efficiency Standards (Energy Code). The standard design features are defined in detail in the Nonresidential and Multifamily Alternative Calculation Method (ACM) Reference Manual.
The performance method is the most detailed and flexible compliance path. The energy performance of a proposed building can be calculated according to actual building geometry and site placement. Credit for certain energy features, such as a high efficiency mechanical system, cannot be taken in the prescriptive approach, but can be evaluated with an approved compliance software program utilizing the performance approach
The ACM Approval Manual describes the application and approval process for submitted compliance software. The ACM Approval Manual is adopted as part of the Energy Standards rulemaking process. The Nonresidential and Multifamily ACM (NRMFACM) Reference Manual is approved by the California Energy Commission (Energy Commission) and includes explanations of the instructions that all compliance software programs must use to model the energy performance of the Proposed Design Building and the Standard Design Building. The reference manual also includes an explanation of the reference method and certification tests used by the Energy Commission to approve compliance software tools. Since the NRMFACM Reference Manual is approved by the Energy Commission (just like the residential and nonresidential compliance manuals), it can be updated from time to time to allow for corrections and enhancements during the 2022 Energy Standards cycle.
The Warren-Alquist Act requires “performance standards” that establish an energy budget for the building in terms of energy consumption per square foot of floor space. This requires a complex calculation of the estimated energy consumption of the building and the calculation is only suited for a computer. The Energy Commission has developed a public domain computer program to do these calculations known as California Building Energy Code Compliance (CBECC). For compliance purposes, The Warren-Alquist Act also authorizes the use of privately developed computer programs as alternatives to the public domain computer program. The public domain computer program and the Energy Commission approved privately developed programs are officially called alternative calculation methods. It is easiest to refer to these programs as "compliance software," which will be the term used throughout this manual.
Compliance software must simulate or model the thermal behavior of buildings including envelope surfaces, lighting, space conditioning, and service water heating systems. The calculations take into account:
- Conductive, convective, and radiative heat gain and loss through walls, roof/ceilings, doors, floors, windows, and skylights.
- Solar radiant heat gain from windows and skylights.
- Heat storage effects of different types of thermal mass.
- Building operating schedules for people, lighting, equipment, and ventilation.
- Space conditioning system operation including equipment part load performance.
- Some covered process mechanical equipment can be modeled (kitchens, laboratories, parking garages, etc.). Details of which covered process equipment is modellable in CBECC are in the NRMFACM Reference Manual.
Compliance software must be approved by the Energy Commission. Approval involves the demonstration of minimum modeling capabilities, required input and output, and adequate user documentation. The compliance software must be able to:
- Automatically calculate the energy budget of the standard design.
- Calculate the energy budget of the proposed design in accordance with specific fixed and restricted inputs.
- Print the appropriate standardized compliance documents with the required information and format when a proposed building complies. Other reports that do not resemble compliance documents may be printed for buildings that do not comply.
Input and output requirements and modeling capabilities are tested by using the compliance software to calculate the energy use of certain prototype buildings under specific conditions. These results are compared with the results from the reference public domain compliance software, CBECC, which uses EnergyPlus as the simulation engine. This is explained in detail in the NRMFACM Reference Manual.
Beginning with the 2005 Energy Standards, the metric or “currency” for assessing building performance has been time dependent valued (TDV) energy. TDV energy replaced annual source energy that had been the compliance metric since the Energy Commission first adopted the Energy Standards in 1978. Starting with the 2022 code cycle, compliance will be based on both TDV and hourly source energy (HSE). For a proposed building to comply, both its TDV and HSE energy use must be less than or equal to the standard design energy budgets. More details on how proposed design energy use and the standard design energy budgets are calculated and how compliance is determined can be found in the NRMFACM Reference Manual and the CBECC or third-party compliance software user’s manuals.
As the name implies, the TDV metric values energy differently depending on the day of the year and hour of the day that a specific type of energy is used. This means that electricity saved on a hot summer afternoon will be worth more in the compliance process than the same amount of electricity saved earlier in the morning when temperatures are mild, HVAC loads are lower, and electricity grid demand for energy is lower. The value assigned to energy savings through TDV more closely reflects the long-term costs for electricity, natural gas, and propane and provides compliance credit for measures that results in load shifting from peak periods to off-peak periods.
Reference Appendix JA3 provides more information on TDV energy. A comparison of TDV energy and flat energy cost are shown below in Figure 12-1.
Figure 12-1: Time Dependent vs. Flat Energy Value
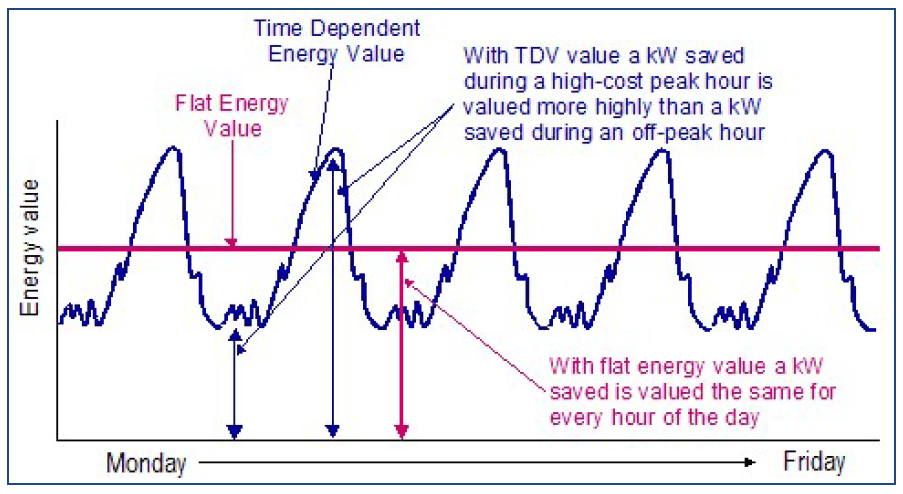
Source: California Energy Commission
HSE is an energy metric for electricity, natural gas, and propane. Put simply, HSE represents the amount of long-term depletable energy resources used to meet the energy demand of the building in each hour. HSE values are very similar to the long-term hourly utility greenhouse gas (GHG) emissions and a strong metric for encouraging building decarbonization.
Because HSE is based on depletable energy use, when renewable resources are used to generate energy, the source energy value decreases for that hour. In hours where renewable resources are scarce, source energy values increase. This means that energy savings during the night, when solar generation is low, is more valuable in HSE than savings during the morning when solar generation is greater.
Certain modeling techniques and compliance assumptions applied to the proposed design are fixed or restricted. That is, there is little or no freedom to choose input values for energy compliance modeling purposes. However, there are other aspects of energy modeling where some professional judgment may be necessary. In those instances, the compliance software user must decide whether a given input is appropriate and will be matched by the actual installation.
Enforcement agencies have discretion to question a particular input if the permit applicant cannot substantiate the value with supporting documentation, cannot demonstrate that appropriate judgment has been applied or cannot demonstrate that the actual installation matches the input.
Simplified modeling approaches can be used if the predicted energy use of the proposed building is not affected or if the proposed energy use increases, reducing the compliance margin when compared to a more explicit and detailed modeling assumption. That is, simplification must reflect the same or higher energy use than a more detailed model and reflect the same or lower compliance margin when comparing the standard and proposed TDV energy and HSE.
Any unusual modeling approach, assumption, or input value should be documented with published data and, when applicable, should conform to standard engineering practice.
Example 12-1
Question
Three different sized windows in the same wall of a new one-story office building are designed without exterior shading, and they have the exact same NFRC-rated U-factors and SHGC values. Is it acceptable professional judgment to simplify the computer model by adding the areas of the three windows together and inputting them as a single fenestration area?
Answer
Yes. For a simplified, two-dimensional, geometry model, the compliance software will produce approximately the same energy results whether the windows are modeled individually or together as one area because the orientation, fenestration U-factors and SHGC values of the windows are identical.
However, if overhangs and side-fins are modeled, the correct geometry of fixed shades must be modeled for each window.
For detailed, three-dimensional, geometry models, the location of windows on walls affects the daylighting energy calculation and this affect must be considered before making the simplification in the example.
For reference, to help determine if you’re using a detailed or simplified approach, a wall in a simplified model will be entered as an area, orientation (i.e., North, South, East, West), height, and width. In a detailed model a wall is entered as a series of points (i.e., x, y, z coordinates) to place the wall in three-dimensional space relative to other surfaces in the building.
This section is a summary of the analysis procedures used to demonstrate building compliance when using approved compliance software programs. Software users and those checking for enforcement should consult the most current version of the compliance software user’s manual and/or on-line help and associated compliance supplements for specific instructions on the operation of the compliance software. Although there are numerous requirements for each software input, the data entered into each software version may be organized differently from one vendor to the next. As a result, it is not possible in this summary to present all variables in their correct order or hierarchy for any one software version. The aim is to identify the procedures used to calculate the standard and proposed design TDV energy and HSE budgets.
Any compliance software version approved by the Energy Commission may be used to comply with the Energy Standards. The following steps are a general outline of the process:
- All detailed data for the building components must be collected including areas and performance properties (i.e., U-factor, SHGC, R-Value, and other thermal properties) for fenestration, walls, doors, roofs, ceilings, floors, and other construction assemblies; and specifications for HVAC and other mechanical equipment, lighting systems, and water heating systems based on the building design plans, drawings, and/or specifications.
- Although most compliance software requires the same basic data, some information requirements, and the way it is organized in the software may vary according to the software used. Refer to the compliance supplement that comes with each version of compliance software for details.
- Prepare an input file that describes the other thermal aspects of the proposed design according to the rules described in the software’s compliance supplement.
- Input values and assumptions must correctly correspond to the proposed design and conform to the required mandatory measures.
- Run the compliance software to automatically generate the energy budgets of the proposed and standard design buildings.
When creating any computer input file, use the space provided for the project title information to describe concisely and uniquely the building that is being modeled. User-designated names should be clear and internally consistent with other buildings being analyzed in the same project. Title names and explanatory comments should assist individuals involved in both the compliance and enforcement process.
The following elements are examples of the information used by compliance software programs to calculate the standard design energy budget and proposed design building energy use. All information entered into the proposed building model, like those shown below, must be consistent with the plans and specifications submitted in the building permit application:
- Opaque Walls: Each opaque exterior wall construction assembly, wall area, orientation, and tilt. Heat capacities, or characteristics necessary to determine the heat capacity (conductivity, mass, volume) of opaque exterior walls, must be included. Interior demising wall area and characteristics must also be input.
- Doors: All doors must be included.
- Opaque Roofs/Ceilings: Each opaque exterior roof/ceiling construction assembly, roof/ceiling area, solar reflectance, thermal emittance, orientation, and tilt. Heat capacity, or characteristics necessary to determine the heat capacity (conductivity, mass, volume) of opaque exterior roof/ceilings, must be included.
- Raised Floors and Slab Floors: Each floor construction assembly, including floor area.
- Fenestrations in Walls and Shading: Each vertical glass area, orientation, tilt, U-factor, Solar Heat Gain Coefficient (SHGC), and Visible Transmittance (VT). Shading from permanently affixed shading devices, such as window overhangs and fins should be included in the model. Shading inputs consist of device depth, distance, and extension relative to the glass.
- Horizontal (Skylight) Fenestration: Each horizontal or skylight glass area, orientation, tilt, U-factor, SHGC, and VT.
- Ventilation Air: Ventilation (introduction of outside air) values in cubic feet per minute (cfm).
- Fan Power: Fan power must be included. Fan power should be based on shaft brake horsepower at the equipment’s rated condition (modeled horsepower must be substantiated by information contained in the construction documents).
- Cooling and Heating Efficiency: The efficiency of the equipment included in the proposed design at AHRI conditions.
- HVAC System Type: The basic type of the cooling and heating system (multiple zones or single zone) and the heating system fuel type (fossil fuel or electric). Note that some projects may have different system types serving separate zones.
- Sensible and Total Cooling System Capacity: Sensible and total output capacity of the cooling system at AHRI conditions.
- Heating System Capacity: The output capacity of the heating system.
- Indoor Lighting: Lighting loads and modeling non-mandatory controls for credit.
- Water Heating: The water heating capacity, volume, and efficiency (including any solar thermal contribution).
- Photovoltaic (PV) and Battery Storage: Required inputs include PV system direct current (DC) size in kW, description of PV system (i.e., standard or premium modules, fixed or tracking array, microinverters or DC power optimizers, solar access percentage), battery system capacity in kWh, and battery system description (i.e., basic or advanced control, and charge/discharge efficiencies and rate)
- Other System Values: All other space conditioning system components, process loads, or any other mechanical system that impacts the building energy performance must be included in the input file.
Refer to the compliance software user’s manual for information on all required modeling inputs and more detailed information on how each input is used by the software.
The TDV and HSE proposed design energy use and standard design energy budgets are separated into compliance totals, which are the basis for building compliance with the performance method, and total building energy use, which adds receptacle, process and other nonregulated energy usage.
The compliance total energy can be summarized into three main components:
- The space conditioning energy use.
- The indoor lighting energy use.
- The service water heating energy use.
Non-regulated energy; process, receptacle, other lighting, and process motors; is treated as compliance neutral. The standard design will always match the proposed energy usage for these categories.
The proposed building energy use is defined by §140.1(b) (Nonresidential) and §170.1(b) (Multifamily) and includes the envelope, space conditioning and ventilation, indoor lighting, and water heating systems assigned to the building. The key component of calculating the TDV energy and HSE use of the proposed building is that if a feature of the building is not included in the building permit application, the energy use of that feature is equal to that of the standard design energy budget defined in §140.1(a) (Nonresidential) or §170.1(a) (Multifamily). That means that if a permit is submitted for a building shell (envelope only), and the performance approach is used to demonstrate compliance, trade-offs cannot be made between the envelope and the mechanical or lighting system.
The standard design budget is defined by replacing all of the energy features of the proposed building with the prescriptive requirements in §140.3 (nonresidential) or §170.2 (multifamily) of the Energy Code. Details of the standard design features are documented in the NRMFACM Reference Manual.
The space conditioning energy budget is automatically determined from the software’s user inputs and the corresponding elements of the proposed design. This budget is automatically re-calculated with each compliance run.
The indoor lighting energy budget consists of the lighting power used by a building based on one of the following criteria:
- When no lighting plans or specifications are submitted for permit and the occupancy of the space is not known, the standard lighting power density is 0.40 W/ft².
- When no lighting plans or specifications are submitted for permit and the occupancy of the space is known, the standard lighting power is equal to the corresponding watt per ft² value derived in the Area Category Method of §140.6(c)2 (Nonresidential) or §170.2(e)3C (Multifamily).
- When lighting plans and specifications are submitted for permit, the standard lighting power is equal to the corresponding total allowed lighting power (in watts) that was used in calculating the proposed lighting level which can be based on either the Area Category Method or the Tailored Method in §140.6(c)2 or 3 (Nonresidential) or §170.2(e)3C or D (Multifamily). A complete set of lighting plans and prescriptive documents are required to use the Tailored Lighting Method in the performance approach. When this method is used to justify an increase in the allowed lighting watts, a lower lighting load in the proposed design cannot be modeled for credit. The standard design building uses the lesser of allowed watts or actual lighting power to be installed in the building. The proposed design building uses the actual lighting power to be installed as detailed on the lighting plans. This value must be equal to or less than the allowed watts.
For all occupancies except hotel guest rooms and multifamily dwelling units, the proposed lighting power is input into the software. For hotel guest rooms or multifamily dwelling units, the compliance software will automatically set the proposed lighting power and the standard design lighting power at the same value as specified in the NRMFACM Reference Manual.
The service and domestic water heating energy budgets consist of the water heating energy used by a building assuming the water heating systems meet both the mandatory and prescriptive requirements for water heating.
The service and domestic water heating standard designs are documented in the NRMFACM Reference Manual.
The performance approach may be used for whole building permit applications; or for permit applications that involve combinations of building envelope, indoor lighting, domestic hot water (DHW)/service hot water (SHW), and/or mechanical systems. The performance method may be used to demonstrate compliance with the envelope or mechanical system alone but can’t be used to show lighting or DHW compliance alone. A permit stage is when less than a whole building is being considered (e.g., the building envelope would be constructed in one permit phase, the mechanical system in another).
Whole buildings are projects involving buildings where the applicant is applying for permits and submitting plans and specifications for all the major components of the building (envelope, mechanical, indoor lighting, and DHW/SHW). This also could be a first-time tenant improvement that involves envelope, mechanical and lighting compliance, where plans and specifications for the entire building are being submitted for permit.
When a whole building is modeled using the performance approach, trade-offs can be made between the envelope, space conditioning, DHW/SHW, and indoor lighting systems that are included in the permit application.
Compliance with only one or more building permit stages can be done using the performance approach except that indoor lighting cannot be done alone. A permit stage is a portion of a whole building permit: either envelope, mechanical, or lighting. This means that trade-offs in energy use are limited to only those features, or a single feature in the case of envelope or mechanical, included in the building permit application. DHW and SHW are not considered a permit stage, but these systems may be optionally included (or not included) in the scope of a performance compliance permit.
When building features are outside the scope of the performance compliance permit, those components will automatically be modeled the same in both the standard design and proposed design by the compliance software. By doing this, the software makes these features compliance neutral; meaning no credit or penalty is given for those features. The NRMFACM Reference Manual and the compliance software user’s manual describe these rules and standard design values in detail.
There are two basic scenarios where a building feature will be outside the scope of a performance compliance permit:
- Modeling future construction features that are not included in the permit application (e.g., future mechanical and lighting systems that are not part of the scope for an envelope only permit).
- Modeling existing construction that has already complied with the Energy Code (e.g., envelope components, that were permitted in an earlier stage of construction, but are not part of the scope for a mechanical and lighting only compliance run).
When a building feature is not included in the performance calculation and permit, that feature will be defaulted automatically by the compliance software. The defaulting rules vary for envelope, mechanical, and indoor lighting. The NRMFACM Reference Manual and software user’s manual contain additional information on these defaulting rules.
Envelope features can’t be defaulted for permitting at a future stage. Usually, the envelope is the first permit for a building and a fully defined envelope is a requirement for calculating the building’s energy budget.
If mechanical is excluded from the scope of the performance permit, in the case of envelope and/or lighting compliance, the default space conditioning system features are determined as described in the NRMFACM Reference Manual for the mechanical system. In general, the compliance software will create a default, minimum efficiency HVAC system, to neutralize mechanical system compliance.
If lighting is excluded from the scope of the performance permit, the default lighting system features depend on whether the occupancy of the space is known. If the space occupancy is known, the allowed lighting power is determined using the Area Category Method for each zone that the occupancy is known. If the space occupancy is not known, 0.40 W/ft² is assumed for both the proposed and standard design buildings.
If DHW and/or SHW are excluded from the scope of the performance permit, the default DHW/SHW system is determined as described in the NRMFACM Reference Manual. In general, a default, minimum efficient DHW and/or SHW system will be automatically created and used in the proposed building model.
When existing indoor lighting or an existing mechanical system is not included in the permit application, the compliance software may use default values for certain inputs. The NRMFACM Reference Manual contains additional information on the default values.
For existing envelopes, there are no automatic defaults. The user must enter details for the existing envelope, i.e., conditioned floor area, glazing, walls, floors/soffits, roofs/ceilings, and display perimeters. Based on the proposed envelope, the software will create a matching standard design envelope. By doing this all existing envelope features are compliance neutral, no credit or penalty.
To model an existing mechanical system, a user can either input the existing space conditioning system; including the type of equipment, actual sizes, and efficiencies; or specify that the existing system is unknown. When the existing system is entered, the compliance software uses the proposed building's space conditioning features to create a matching standard design mechanical system. This means that all existing mechanical systems in the proposed model are compliance neutral, no credit or penalty. When the system is unknown, the software will automatically create a minimally efficient HVAC system in the proposed design.
The default service water heating system is determined as described in the NRMFACM Reference Manual and will only be listed as "Existing".
Existing lighting system features are based on the known occupancy of the building and whether information on the existing system is known. The lighting power entered for the proposed model is determined based on either the Area Category lighting power allowances for the proposed design occupancies, or if the existing design lighting power is known the actual design data should be entered instead. The compliance software then creates a standard design matching the proposed design so that compliance is neutral, no credit or penalty, for the existing lighting system.
An addition that consists of both new conditioned floor area and added volume will either need to comply as an addition alone or as an existing plus addition plus alteration. For the addition alone path, the same requirements for a newly constructed building will apply to the addition. All systems serving the addition will require compliance to be demonstrated; and either the prescriptive or performance approach can be used for each stage of the construction of the addition. Existing plus addition plus alteration requires modeling of the existing, altered, and new components, but gives the opportunity for compliance tradeoffs between the new and altered components in the addition and existing building.
When existing space conditioning or water heating is extended from the existing building to serve the addition, the existing components of these systems should be modeled as existing and the new components of these systems must be modeled as new (e.g., new ducts extended to the addition) so that the software can determine the correct standard design based on section 141.0(a) (Nonresidential) or 180.1 (Multifamily).
Additions that show compliance with the performance approach independent of the existing building must meet the requirements for newly constructed buildings. §141.0(a) (Nonresidential) and §180.1 (Multifamily) state that the envelope and indoor lighting of the addition, and any newly installed space conditioning, electrical power distribution system, or water heating system must meet mandatory measures and the applicable energy budget:
- If the permit is done in stages, the rules for each permit stage apply to the addition’s performance run.
- If the whole addition (envelope, lighting and mechanical) is included in the permit application, the rules for whole buildings apply.
Additions may also show compliance by either:
- 7. Demonstrating that efficiency improvements to the envelope component of the existing building, as well as certain indoor lighting and mechanical improvements, offset addition performance that would otherwise not meet the energy budgets for the addition alone (see §141.0(a)2Bii (Nonresidential) or 180.1(b)2 (Multifamily)).
For additions, the most flexible compliance method is to consider the entire existing building along with the addition (Existing + Addition + Alteration).1 The combination of additions and alterations to the existing building may be shown to comply by demonstrating that the proposed design energy use is equal to or less than the standard design energy budget based on the alterations meeting the requirements of §141.0(b)3 (Nonresidential) and §180.2(c) (Multifamily) and additions meeting the requirements of §141.0(a)2 (Nonresidential) or 180.1(b) (Multifamily). Additionally, §141.0(a)2 (Nonresidential) and 180.1(b) (Multifamily) state that the envelope and indoor lighting in the conditioned space of the addition, and any newly installed space conditioning, electrical power distribution system or service water heating system, must meet the mandatory measures.
This approach allows the applicant to improve the energy efficiency of the existing building so that the entire building meets the energy budget that would apply if the existing building were unchanged, and the addition complied on its own. Changes to features in the existing building are considered alterations.
For a full description of when and how altered components in the existing building are counted as a credit or penalty in the performance calculation, as well as basic energy modeling rules for alterations, see the Alterations Performance Compliance section 12.5.4 below.
1This method may also be used whenever an alteration is made to existing buildings, whether or not there is an addition to the building at the same time.
Example 12-22
Question
3,000 ft² of conditioned space is being added to an existing office building. 25% of the lighting fixtures in the existing office space are being replaced with more efficient fixtures. Can credit be taken for the improved lights in the existing building to comply through the existing-plus-addition performance approach?
Answer
Since 10% or more of the lighting fixtures are replaced, all prescriptive lighting alteration requirements must be met. Credit can only be taken for lighting efficiency improvements resulting in a lower lighting power than is required to meet §140.6 (Nonresidential) and §170.2(e) (Multifamily).
Using the performance approach for an alteration is similar to demonstrating compliance for an addition.
Altered spaces can show compliance with the performance approach independent of the remainder of the existing building but must still meet the requirements for the altered components of the building as specified in §141.0(b)2 (Nonresidential) and §180.2(a) (Multifamily). These require that envelope and lighting alterations, as well as any new or replacement space conditioning or service water heating system serving the alteration, meet the mandatory measures. The permitted space alone may comply with the energy budget determined using approved compliance software.
If the permit is done in stages, the rules for each permit stage apply to the alteration performance run.
Alterations may also show compliance by demonstrating that the energy use of the proposed design -- including all energy efficiency improvements to the existing building -- is equal to or less than the standard design energy budget which is based on the alterations meeting the requirements of §141.0(b)2 (Nonresidential) and §180.2(a) (Multifamily) and Table 141.0-E (Nonresidential) of the Energy Code. Note that §141.0(b)1 (Nonresidential) and §180.2(a) (Multifamily) also require that envelope, lighting, space conditioning and service water heating system alterations meet the applicable mandatory measures.
This approach allows the applicant to improve the energy efficiency of the existing building so that it meets the energy budget that would apply to the entire building if the existing building other than the portion being altered was unchanged. Changes to features in the existing building are considered alterations.
An energy penalty is assigned to any altered component that does not meet or exceed the requirements of §141.0(b)2 (Nonresidential) or §180.2(b) (Multifamily). A credit is assigned to an alteration (improvement) that exceeds the requirements in §141(b)2 (Nonresidential) or §180.2(b) (Multifamily) as summarized in Table 141.0-E (Nonresidential) of the Energy Code and further detailed in the NRMFACM Reference Manual. For Nonresidential, the compliance software sets the standard design for the altered component as listed in Table 141.0-E of the Energy Code and for multifamily the software sets the standard design based on the requirements of §180.2(b).
This compliance approach includes the entire building which means the ensemble of all enclosed space in a building, including the space for which a permit is sought, plus all conditioned and unconditioned space within the structure. The inclusion of the characteristics of unconditioned spaces have an effect on the overall performance budget of the building due to the loads of the unconditioned spaces adjacent to the conditioned spaces which can be beneficial or detrimental to the overall compliance margin.
When using this compliance approach, it is important to take into account all changes in the features of the building that are:
- EXISTING (that remain unchanged).
- ALTERED (improved or replaced).
- NEW (all new).
Note that surfaces which are being completely removed from the existing building – roofs/ceilings, exterior walls and floors, and all glazing removed with those removed surfaces – are not modeled.
To show compliance with this approach you need to follow the instructions in the compliance software user’s manual. Documentation of the existing building’s glazing areas is required to be submitted with the permit application if this method is used for replacement fenestration credit.
Example 12-3
Question
Alterations to an existing office building in Climate Zone 12 includes replacing all single clear metal frame operable windows with new NFRC-rated windows (U-factor =0.45, SHGC=0.31.) What standard design values will the compliance software use for the replacement fenestration area?
Answer
The standard design will use the values in Table 141.0-A (U=0.47, SHGC=0.31 and VT=0.32) of the Energy Standards regardless of whether the replacement windows’ values exceed those Table 141.0-A values of the Energy Standards.
See Existing Plus Addition Plus Alteration section in this chapter.
Any addition, alteration or repair may demonstrate compliance by meeting the requirements applicable to newly constructed buildings for the entire building. Using this method, the entire building could be shown to comply in permit stages or as a whole building. The rules for new buildings permit stage compliance (Section 12.5) and whole building compliance (Section 12.5.1) would apply.
Documentation of the existing building’s features is required to be submitted with the permit application if this method is used.
At the time a building permit application is submitted to the enforcement agency, the applicant also submits plans and energy compliance documentation. This section describes the documents and procedures for documenting compliance with the performance requirements. The NRMFACM Reference Manual has specific and detailed output/reporting requirements for all approved compliance software.
Compliance software output is required to specify the run initiation time, a unique run code, and the total number of pages of documents printed for each proposed building run on each page whenever a building complies with the Energy Code. The plan checker is strongly encouraged to verify these output features for a performance compliance submittal to ensure that the submittal is a consistent set of compliance documentation. The NRMFACM Reference Manual forbids compliance software from printing valid compliance documents for a proposed building design that does not comply. The plan checker should pay special attention to the PRF-1 document and the Exceptional Conditions List on that document. Every item on the Exceptional Conditions List deserves special attention and may require additional documentation, such as manufacturer's cut sheets or special features on the plans and in the building specifications.
The compliance software requirements will automatically produce and reiterate the proper set of documents that correspond to the proposed building submitted for a permit. However, the plan checker should verify the type of compliance and the required documents. Whenever an existing building or existing building components are involved in the compliance calculation, the plan checker should look for the term EXISTING that identifies EXISTING building components that remain unchanged. Similarly, if the compliance document indicates a component is ALTERED these changes should be verified. In permit applications where some building components are unknown, the unknown components cannot be entered by the user and cannot be reported on output documents. The PRF-01 document will show all the pertinent information required for a complete submittal.
The compliance documents associated with the performance approach are generated automatically and the entire printout is called the PRF-01.
Unless minimal efficiency and default capacities are used in the performance analysis, design drawings or specifications must be provided to document the differences in the capacities and efficiencies of the proposed equipment.
Other documentation supporting each non-standard or non-default value used in the performance approach and indicated in the Exceptional Conditions list on the PRF-1 document must also be included.
Performance approach inspection is identical to other inspections required by the Energy Standards. For information on inspection of envelope, mechanical and lighting systems, refer to Chapter 2, Compliance and Enforcement.